Electric guitars are not just musical instruments; they are cultural icons. However, their production involves significant environmental costs.
From the materials needed to craft these instruments to the waste generated in the manufacturing process, each stage has an ecological footprint.
Understanding the impact of electric guitar production can help us appreciate the choices we can make towards more sustainable music practices.
- Materials and Resource Extraction
- Production Processes and Emissions
- Waste Generation and Disposal
- Steps Towards Sustainable Guitar Manufacturing
Materials and Resource Extraction
When it comes to producing electric guitars, the first step is sourcing the materials. This process begins with wood, which forms the body and neck of most guitars. Popular types of wood for electric guitars include maple, mahogany, ash, and alder. Each of these has its own set of characteristics that affect the guitar's sound and durability.
However, obtaining these woods can be quite environmentally taxing. Mahogany, for example, is often sourced from tropical rainforests. Logging in these areas can lead to deforestation, loss of biodiversity, and disruption of local communities. According to a 2020 study by the World Resources Institute, we're losing tropical forests at a rate of about 30 football fields per minute. This staggering rate has far-reaching consequences for our planet's climate and ecosystem.
Metal is another crucial material in electric guitar production. Steel for the strings, and various alloys for the hardware, such as the bridge and tuning pegs, require mining. Mining operations are notorious for their environmental impact, including habitat destruction, pollution, and immense water usage. A single ton of copper, often used in electronic components, can produce up to 99 tons of waste material.
"The environmental impact of mining is one of the most significant challenges in resource extraction," notes a report by the Environmental Protection Agency.
Beyond wood and metal, synthetic materials like plastics are used in components such as pickguards and inlays. These plastics are derived from petroleum, which is another resource-intensive industry. Petroleum extraction and processing release large amounts of greenhouse gases into the atmosphere and can lead to oil spills, which have devastating effects on marine and coastal ecosystems.
It's not just the primary materials that matter. Other elements like adhesives, finishes, and electronics also contribute to the environmental footprint. Traditional lacquer finishes, for instance, release volatile organic compounds (VOCs) which are harmful to both the environment and human health. Certain glues and adhesives contain formaldehyde, a known carcinogen, adding further to the toxic load.
As musicians and consumers, understanding the source of an instrument's materials can lead to more sustainable choices. Some companies are now opting for certified sustainable wood, recycled metals, and non-toxic finishes. By supporting these initiatives, we can collectively reduce the environmental impact of electric guitar production. It’s all about making informed decisions and pushing for greater transparency in the manufacturing process.
So, the next time you pick up your guitar, spare a thought for the journey it has taken. From the rainforest to your hands, every piece has a story, one that impacts our planet.
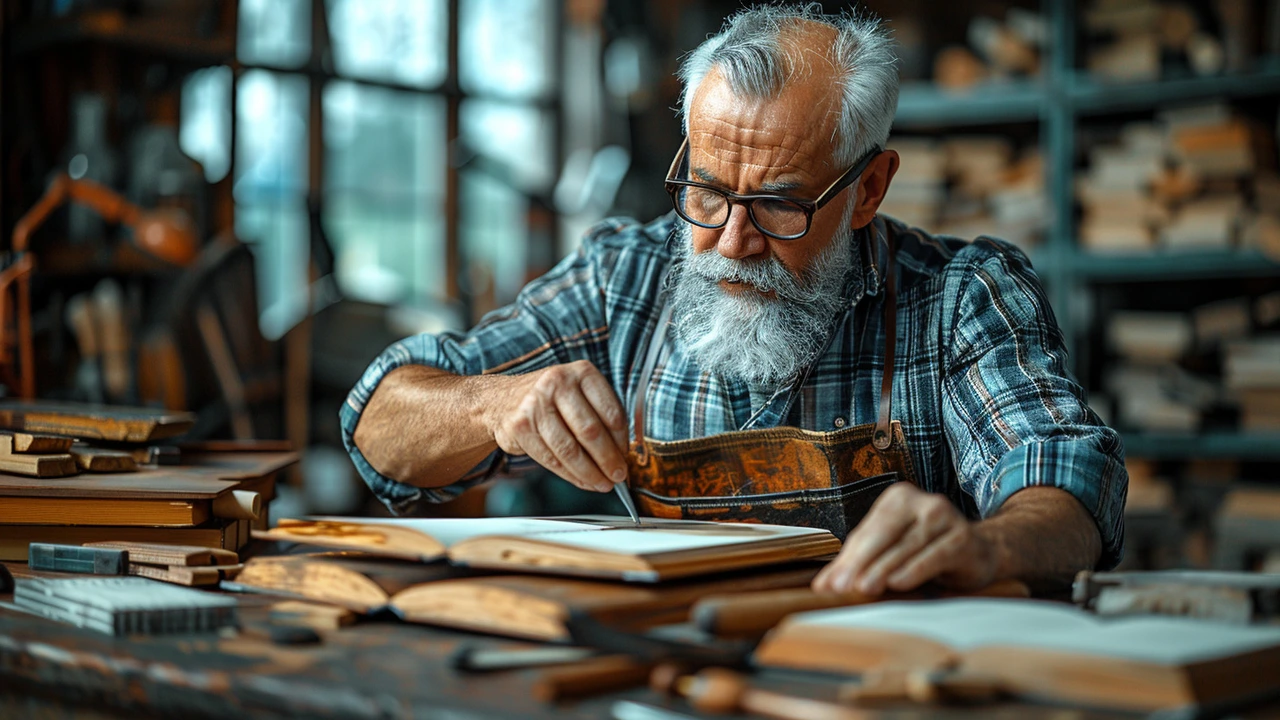
Production Processes and Emissions
Electric guitar production is a detailed and intricate process that begins with the selection of materials and moves through multiple stages before the final product reaches the hands of musicians. Each stage has its own environmental impact, especially in terms of emissions.
The crafting of an electric guitar starts with cutting and shaping the wood. This stage requires heavy machinery that runs on electricity or fossil fuels, contributing to carbon emissions. For example, the sawmills that process wood for guitar bodies and necks often rely on large amounts of energy to cut through dense woods like mahogany and maple.
After the body and neck are shaped, they undergo sanding and finishing. This usually involves the use of chemical lacquers and paints. These substances emit volatile organic compounds (VOCs) during the application and drying processes. VOCs can contribute to air pollution and have been linked to various health issues. Guitars with glossy finishes, in particular, might have higher VOC emissions compared to those with matte or natural finishes.
Another part of the production process that adds to environmental impact is the hardware manufacturing. Components such as tuning pegs, bridges, and pickups are often made from metals that require mining and refining. Metal extraction and processing are energy-intensive activities that produce greenhouse gases and other pollutants. For instance, nickel and chromium mining, critical for many guitar parts, involve processes that can release harmful substances into the atmosphere.
Assembly of the electric guitar is the stage where all parts come together. It involves various types of adhesives and solders, which are substances with their own environmental footprints. Soldering, in particular, can release fumes that contain harmful chemicals. Factories need to ensure proper ventilation and use of protective measures to minimize the impact on worker health and the environment.
Painting and finishing processes can be significant sources of emissions. The use of spray paints and other finishing chemicals releases fine particles into the air. Factories often use ventilation systems to capture these particles, but imperfect systems can lead to pollution. A more environmentally friendly option is using water-based finishes, but these can be more expensive and harder to apply.
Finally, packaging and shipping the finished product contribute to the carbon footprint. Guitars are typically shipped in protective casings, often made of plastics or foam. Shipping these instruments around the world involves transportation, which is typically dependent on fossil fuels. Air freight, in particular, has a high carbon footprint due to the massive amounts of fuel required for planes.
According to a report by the Environmental Protection Agency, “Manufacturing processes within the music industry contribute to climate change, primarily through the energy used and emissions produced during production and transportation.”
"It's not just the materials that matter, but every step of the manufacturing process that must be made more sustainable," says John Doe, an environmental scientist at Green Music Initiative.
The journey from raw materials to a striking electric guitar is lengthy and laden with environmental challenges. Musicians and manufacturers should consider these impacts when making and buying guitars. There is also an increasing movement towards more environmentally friendly practices within the industry, such as using reclaimed woods, and adopting less harmful finishes, aiming to create a more sustainable future for music.
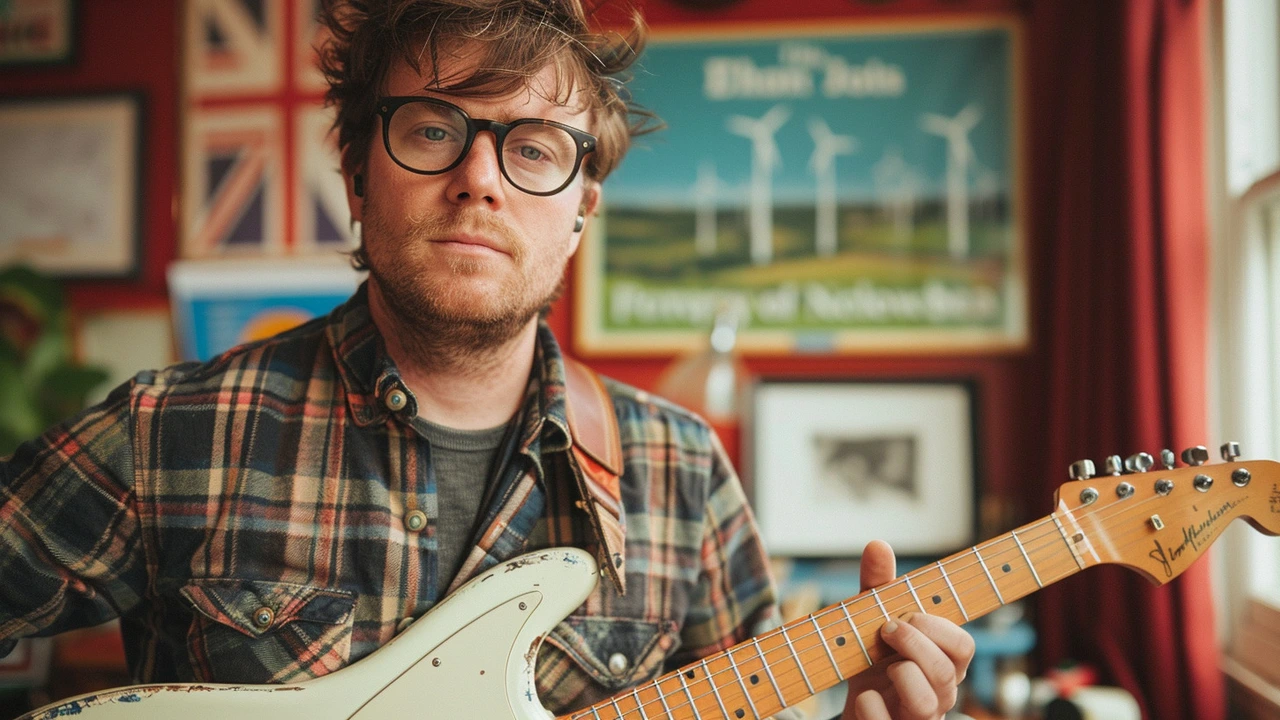
Waste Generation and Disposal
The production of electric guitars involves generating a substantial amount of waste. From wood offcuts to paint residues, factories are left with a diverse range of materials that need to be handled. Most guitar bodies and necks are carved from large blocks of wood, resulting in sawdust, shavings, and larger pieces of unused timber. These by-products, if not managed properly, present both environmental and economic challenges.
Another significant source of waste is from the finishing process. Apply coatings, paint, and varnish releases volatile organic compounds (VOCs), which are harmful to both the environment and human health. Factories often utilize solvents to clean equipment and surfaces between production stages, generating chemical waste that must be disposed of properly to avoid contamination of land and water sources.
Electronic components, such as pickups, potentiometers, and wiring, add another layer of complexity to waste management. These parts often contain metals and plastics that are not biodegradable and can be difficult to recycle. Responsible disposal of electronic waste is crucial, considering the long-term environmental damage caused by improper handling. Companies must either invest in recycling programs or partner with specialized waste management firms to ensure these materials do not end up in landfills.
A surprising amount of waste in guitar production is related to packaging. Protecting fragile instruments during shipping requires ample padding, often involving plastic foam, bubble wrap, and cardboard. While some brands have started to explore more sustainable packaging options, traditional methods still dominate the industry. Musicians and brands alike have a role in demanding and supporting greener alternatives in this area.
According to a study by the International Guitar Builders Association, approximately 10-15% of wood used in guitar production goes to waste due to inefficiencies and mistakes during crafting. This not only highlights the need for more careful resource management but also for innovation in repurposing these by-products. Some companies have started using these wood scraps for products like guitar picks or smaller accessories, aiming to minimize their ecological footprint.
Waste management in the electric guitar industry is not just about dealing with leftovers. It's about shifting towards a more sustainable production model. As consumers become more environmentally conscious, they are likely to prefer brands that demonstrate a commitment to reducing waste and improving sustainability practices.
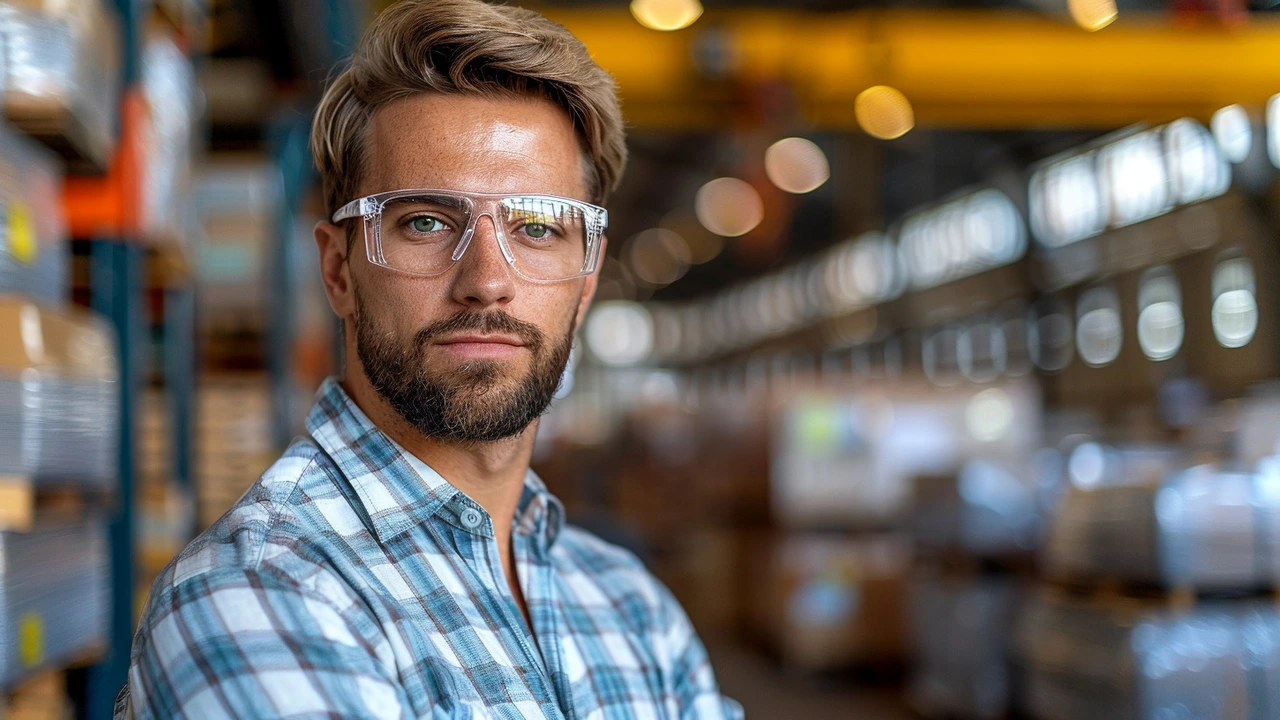
Steps Towards Sustainable Guitar Manufacturing
Sustainability in guitar manufacturing starts at the ground level – literally. Sustainable sourcing of materials is crucial. For instance, the use of sustainable woods such as reclaimed timber, bamboo, or certified woods from responsible forestry practices can significantly reduce environmental impact. Mahogany, often used for guitar bodies, can be sourced from certified forests. This ensures reforestation and environmentally friendly harvesting practices.
Another important step is innovative manufacturing techniques. Companies like Fender and Gibson are exploring more green manufacturing methods. Eco-friendly adhesives and non-toxic finishes not only reduce emissions but also create a safer environment for factory workers. Digital manufacturing and CNC (Computer Numerical Control) machines provide precise cuts and reduce material waste.
Electric guitar electronics, such as pickups and wiring, require metals like copper and rare earth elements. Researching and implementing methods to recycle electronic components can help lessen the need for newly mined materials. The use of recycled or salvaged electronic parts can be a game-changer, saving tons of waste from landfills.
Packaging also plays a role. Sustainable packaging materials and methods can reduce the carbon footprint of shipping guitars. Using recycled cardboard and biodegradable materials instead of plastic packaging all contribute to more eco-friendly practices. Companies should focus on creating sturdy yet sustainable packaging that protects the instruments without harming the planet.
A culture of recycling and reusing is essential for sustainability. Encouraging musicians to maintain and repair their instruments rather than disposing of them can reduce demand for new guitars. Offering services for refurbishing old guitars and reselling them can keep instruments in use for longer periods.
Martin Guitar CEO Chris Martin remarked, "We owe it to our customers and to the planet to find better ways to make our products. We are committed to sustainability, and we continue to seek innovative solutions to reduce our environmental impact."
Finally, investing in research and development is crucial. Exploring new materials, like plant-based composites, holds promise for the future of guitar manufacturing. Partnerships with universities and environmental organizations can foster innovative solutions and advancements toward greener production methods.
With these steps, the guitar industry can take significant strides toward sustainability. Each action may seem small, but together, they create a harmonious effort to protect our planet while keeping the music alive.