In recent years, the acoustic guitar manufacturing industry has embraced a surge of innovation, blending age-old techniques with modern technology. This fusion has opened the door to new possibilities in sound quality and design.
Gone are the days when traditional wood types were the sole choice in guitar building; today's luthiers are experimenting with alternative materials like carbon fiber and even reclaiming wood from centuries-old sources. These materials not only enhance sound but also promote sustainability.
3D printing stands out as another innovation that's fostering creativity and efficiency in guitar crafting. It enables precise customization and experimentation that were previously unimaginable.
Equally important are the advancements in sound-enhancing technology, where integrated electronics and innovative bracing systems are driving the evolution of how acoustic guitars resonate.
- Evolution of Materials
- 3D Printing and Acoustic Guitars
- Technological Advancements in Sound Quality
- Eco-Friendly Production Methods
Evolution of Materials
The world of acoustic guitar manufacturing has dramatically transformed as artisans and engineers alike have turned to novel materials to craft these beloved instruments. Gone are the days when mahogany and rosewood reigned supreme, as the industry experiences a renaissance reminiscent of the shift from steam to digital. Modern luthiers are exploring materials like carbon fiber and high-pressure laminate (HPL), offering a fresh take on what was once rooted in tradition. This innovation doesn't merely aim to replace traditional woods but seeks to enhance the guitar's sound and longevity while addressing pressing environmental concerns.
Carbon fiber, for example, has taken center stage in some innovative guitar designs. It's a material known for its strength-to-weight ratio, providing unmatched durability and a consistent sound that doesn't warp under changing weather conditions. This reliability makes it an attractive option for musicians who travel extensively, ensuring their instruments maintain their pitch and tone regardless of humidity and temperature shifts. While some purists may hesitate, those who have tried carbon fiber guitars often rave about their robust sound and resilience.
Another exciting venture has been the incorporation of reclaimed wood in guitar crafting. Builders are scavenging everything from old barns to submerged logs, giving life to materials that have stood the test of time. These woods bring unique characteristics and stories, infusing each note played with history. Moreover, they speak to an increasing demand for eco-friendly production methods, a trend that resonates with current and future generations of musicians. Famous guitar makers have started limited runs of these sustainably sourced guitars, each with a certificate detailing its lineage, adding a collectible aspect to their allure.
According to master luthier Andy Powers, "The path towards sustainable guitar building is paved with many trials and errors, but each experiment brings us closer to crafting instruments that will echo in harmony with our planet."
This shift is not just about sustainability; it's also about tapping into innovative sound possibilities. When paired with modern technologies such as 3D printing, the use of alternative materials allows for design experimentation that can significantly influence the acoustic properties of each instrument. In essence, every evolution in material selection offers its own promise for the future of music, blending creativity with responsibility in equal measure.
Material | Benefits | Challenges |
---|---|---|
Carbon Fiber | Durability, Weather Resistance | Cost, Traditionalists' Skepticism |
Reclaimed Wood | Sustainability, Unique Sound | Limited Availability, Consistency |

3D Printing and Acoustic Guitars
The world of acoustic guitar crafting is undergoing a quiet revolution with the advent of 3D printing technology. This innovation is allowing luthiers to push the boundaries of design and sound in ways that were previously unimaginable. By layering materials in precise patterns, craftsmen can create complex structures that influence the guitar's acoustics. 3D printing provides a level of customization that traditional methods can't match, enabling fine-tuning of the instrument’s tone, volume, and sustain.
The process begins with a computer-aided design (CAD) model of the guitar, which can be tweaked to perfection before printing starts. This level of precision means that every aspect of the guitar can be meticulously planned to achieve the desired sound. Material selection is also a game-changer; while traditional guitars rely on a limited range of woods, 3D printing opens the door to using innovative materials such as carbon fiber and nylon composites. These materials can mimic wood's acoustic properties while offering greater durability and resistance to environmental changes.
3D printing also reduces wastage, as it uses only the materials necessary for the object. This attribute is not only cost-effective but also environmentally friendly, a key consideration for modern manufacturers. Additionally, this method allows for rapid prototyping, meaning new designs can be tested in days rather than months. Innovators can experiment with different body shapes, internal bracing patterns, and neck designs to find the perfect balance between aesthetics and function. The speed of iteration brings new guitars to the market quicker, fostering a cycle of constant innovation.
Interestingly, some avant-garde manufacturers are using 3D printing to produce specific components of the guitar, such as the bridge or the tuning pegs, which can then be combined with traditionally crafted parts. This hybrid approach takes advantage of the strengths of both worlds. The potential for 3D printing in guitar technology is immense, and we are only scratching the surface of what could be achieved. This blend of old-world artisanship and futuristic technology makes each guitar a unique piece of art. A renowned luthier was quoted saying, “3D printing doesn't replace the guitarist's soul; it just gives it a new, vibrant voice.”
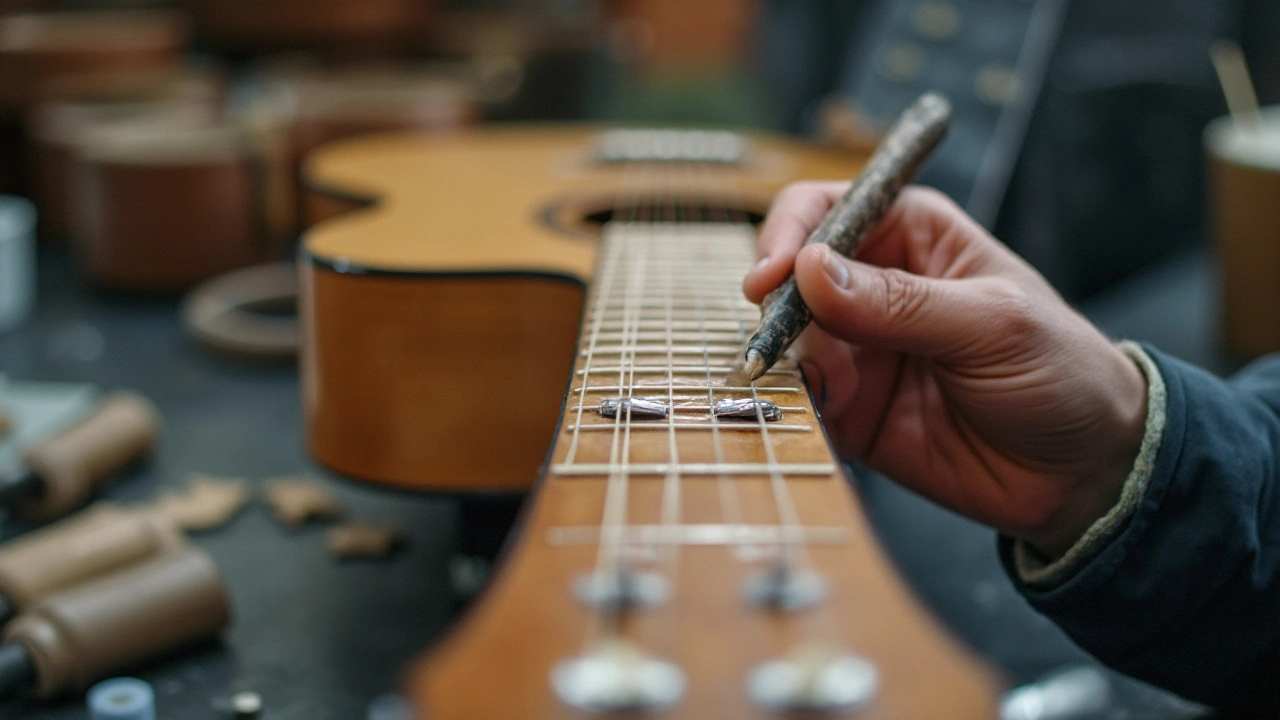
Technological Advancements in Sound Quality
The realm of acoustic guitar manufacturing is deeply intertwined with the pursuit of perfect sound. In recent years, technological advancements have reached new heights, allowing manufacturers to produce instruments that can both preserve the traditional tonal qualities and introduce modern enhancements. One fascinating development is the use of laser technology to fine-tune the resonant frequencies of the guitar's soundboard. This precision trim, achieved through non-invasive methods, enhances the overall tonal balance and improves projection. Luthiers can now sculpt sound characteristics with pinpoint accuracy, which was a dream just a few decades ago.
One cannot overlook the role of computer-aided design and simulation software in revolutionizing how the acoustic properties are assessed and improved. These tools allow designers to experiment with various bracing patterns and body shapes virtually before committing them to physical prototypes. This software-driven approach results in guitar crafting that is both efficient and innovative. Adjustments that would have taken weeks can now be implemented in days, thereby reducing production time and enhancing sound quality substantially. In a conversation with Guitar World, master luthier Richard Hoover once remarked, ". . . technology doesn't replace skill; it gives us more ways to express it.” This fusion of technology and craftsmanship indeed creates a harmonious balance between tradition and innovation.
Moreover, preamp systems embedded with advanced signal processing capabilities now allow acoustic guitars to produce sound that is faithful to their unplugged tone even when amplified. These onboard electronics offer players the flexibility to adjust tone settings without sacrificing the guitar's natural acoustic characteristics. This technology is especially prized by gigging musicians who rely on both the purity of sound and ease of use during performances. Some systems even incorporate feedback suppression, a long-standing issue for amplified acoustic guitar performances, ensuring a cleaner sound profile no matter the setting. Such systems are a testament to how electronics are being adeptly intertwined with acoustic guitar design.
Data suggest current consumers are highly tech-savvy and appreciate the possibility of adjusting their instrument’s capabilities. Studies conducted by the music tech industry show that about 75% of new guitar buyers are keen on models that include modern technological enhancements. Manufacturers are taking note of this trend, offering more models with integrated digital interfaces that allow seamless connection to apps and software for tone shaping and recording. It's clear that as guitar technology continues to evolve, the focus remains on crafting experiences that resonate with both new and seasoned musicians alike.
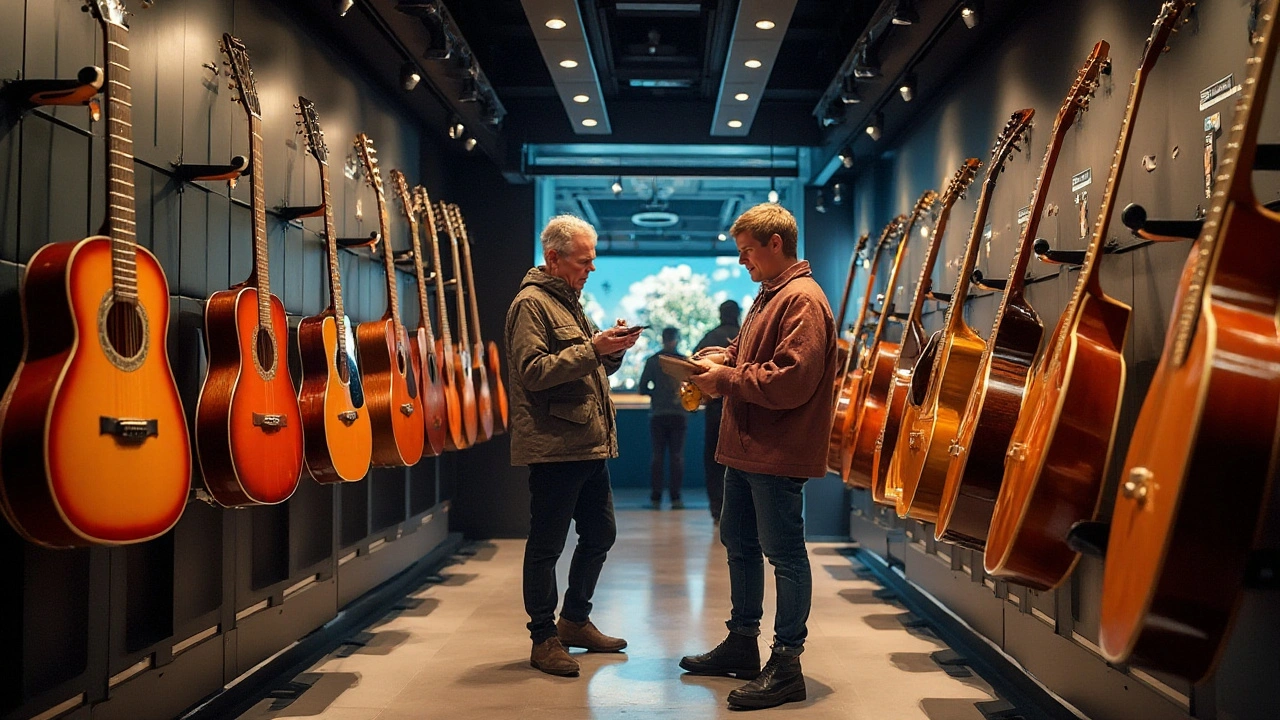
Eco-Friendly Production Methods
The journey toward eco-friendly production methods in acoustic guitar crafting is not just a trend but a pivotal movement responding to the increasing environmental concerns across industries. Guitar makers are now focusing on sustainable practices to reduce their ecological footprint and craft instruments that are as kind to the earth as they are pleasing to the ear. This shift involves a reevaluation of materials, techniques, and processes traditionally used in the industry. By choosing responsibly sourced woods or alternative materials like bamboo and hemp, manufacturers aim to minimize deforestation and preserve biodiversity. Such materials not only match the firmness and flexibility of traditional wood but also offer unique tonal qualities, giving artists more choices when crafting their sound.
Embracing renewable energy and reducing waste are also central to these eco-friendly strategies. Some guitar makers have shifted to solar-powered factories and implemented rigorous recycling systems to ensure that excess materials are repurposed rather than discarded. A few innovative companies even utilize reclaimed wood from old structures such as barns or bridges, breathing new life into what would otherwise be waste. This approach not only highlights craftsmanship but also centuries of musical evolution, as each piece carries with it a story of its past. Using recycled materials often enhances the resonant quality of guitars, adding a richness to their sound that new materials cannot replicate.
The move towards sustainability is not without its challenges. Balancing the demands of maintaining quality and environmental responsibility requires collaboration and innovation at every level. This complexity is underscored by the need for certain detailed craftsmanship which, unlike mass production, cannot be hurried. Renowned luthier Bob Taylor, of Taylor Guitars, emphasized, "Taking care of the forest means taking care of the future of music," highlighting the industry's commitment to protecting natural resources. This philosophy carries weight, encouraging manufacturers to adopt practices such as promoting the growth of native tree species so that both the industry and the environment can prosper.
Educating consumers also plays a significant role. As players become more conscious of the environmental impact of their artistic choices, they demand transparency from brands. By showcasing sustainable methods and engaging directly with musicians, companies not only build trust but also spark greater demand for greener alternatives. Consumers learn not only about the origin of the materials but also about the efforts involved in ensuring environmental safety during production. This wave of awareness signals a cultural shift where art and ethics intertwine, creating a ripple effect that influences future generations of both musicians and consumers.